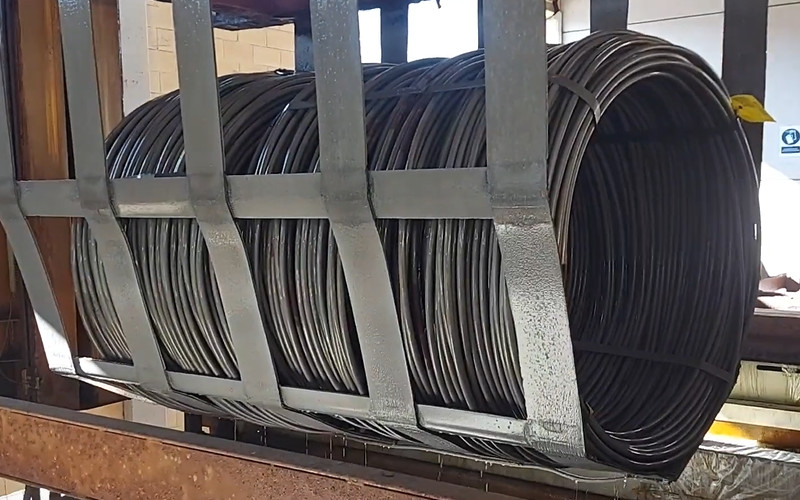
Raw material
We have a pickling facility for the preparation of raw material, as well as for the drawing of raw material, being able to draw steel from 6 mm to 22 mm in diameter.
We have a pickling facility for the preparation of raw material, as well as for the drawing of raw material, being able to draw steel from 6 mm to 22 mm in diameter.
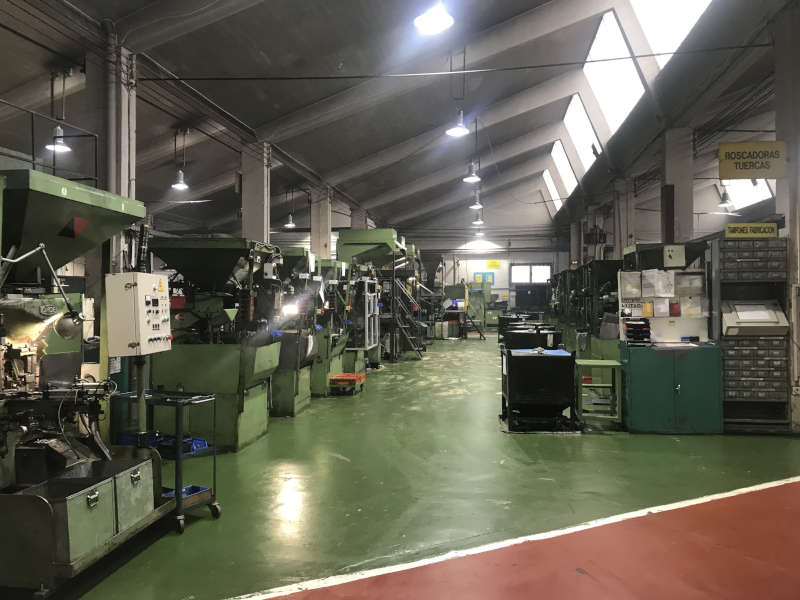
Nut stamping
We currently have a total of ten 5-station stamping machines, with a cutting diameter of up to 22 mm. This allows us to manufacture nuts of different, highly complex geometry.
We currently have a total of ten 5-station stamping machines, with a cutting diameter of up to 22 mm. This allows us to manufacture nuts of different, highly complex geometry.
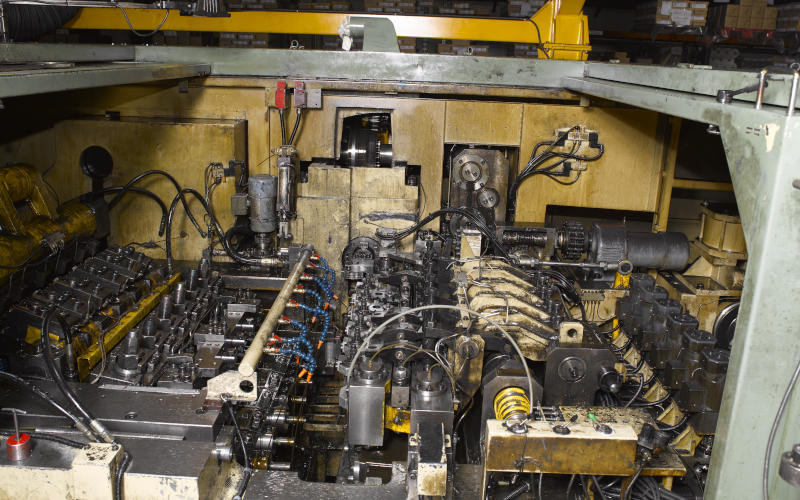
Stamping of special parts
For the manufacture of special parts we have invested in three 6-station machines, one of which has a cutting diameter of up to 30 mm.
For the manufacture of special parts we have invested in three 6-station machines, one of which has a cutting diameter of up to 30 mm.
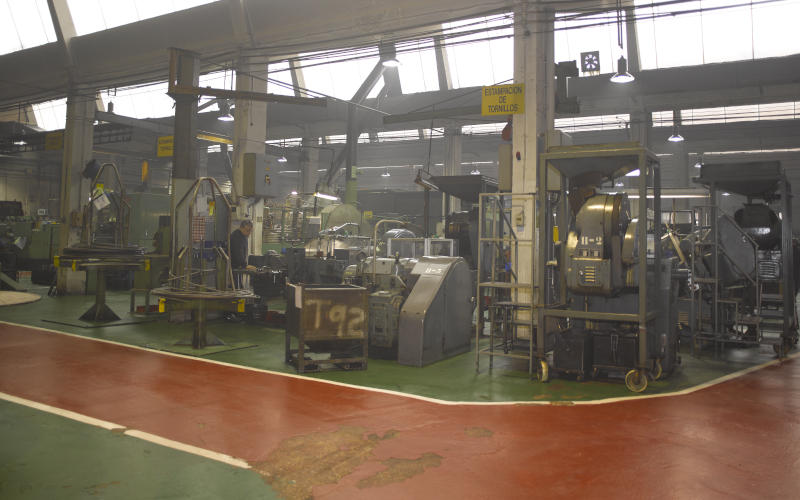
Screw stamping
Our three screw machines, two of which have 4 stations, allow us to manufacture a range from M6 to M16, both standard and special.
Our three screw machines, two of which have 4 stations, allow us to manufacture a range from M6 to M16, both standard and special.
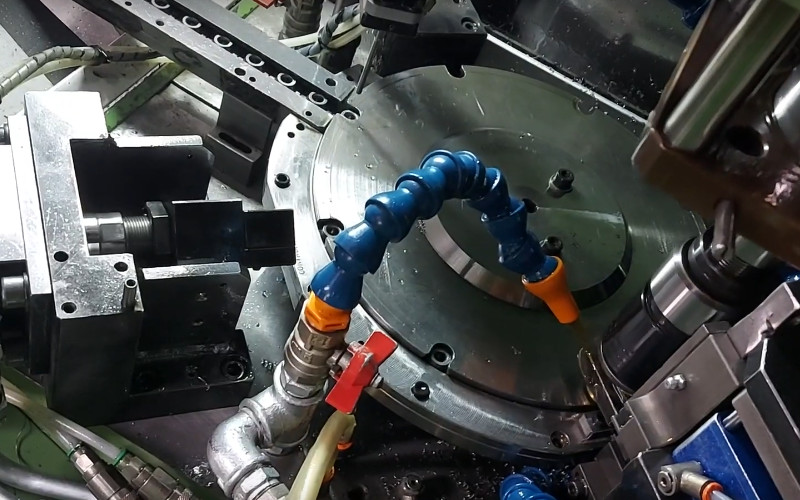
Threading
As for the threading of parts, there are twenty-two machines dedicated to this operation, six of which are for special parts, being able to thread up to M20.
As for the threading of parts, there are twenty-two machines dedicated to this operation, six of which are for special parts, being able to thread up to M20.
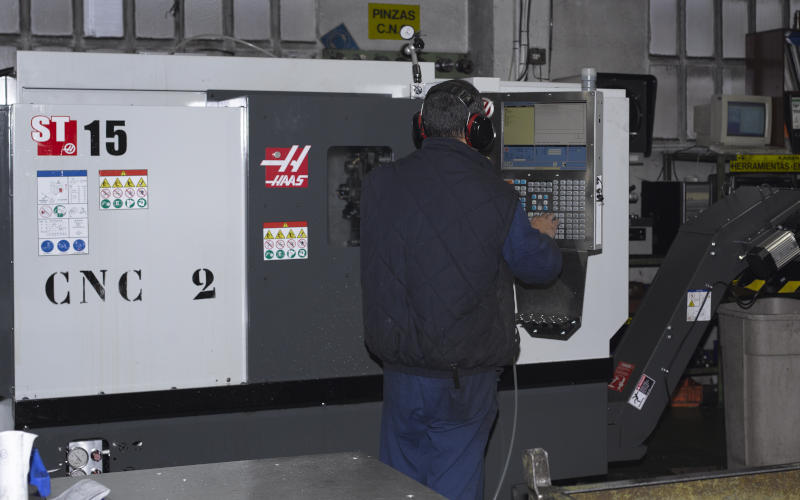
Mechanical workshop
For the manufacturing of part of our own tooling, we have a machining workshop, which allows us to be more agile and responsive to any emergencies that may arise.
For the manufacturing of part of our own tooling, we have a machining workshop, which allows us to be more agile and responsive to any emergencies that may arise.
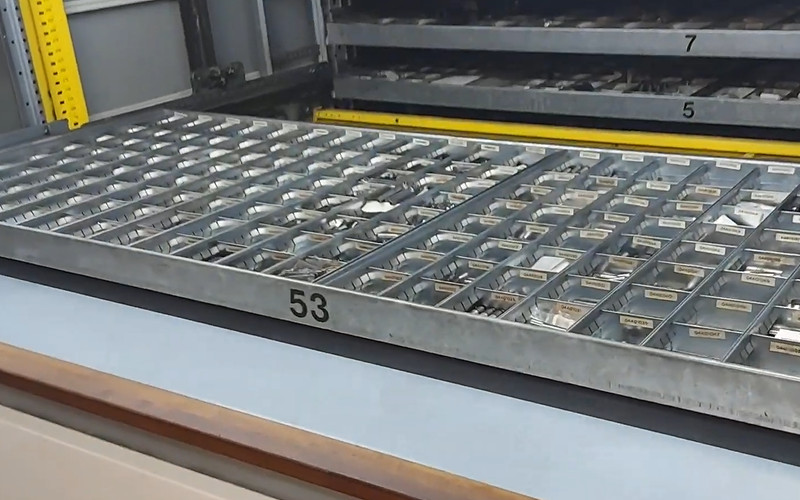
Tool storage
We manage and control the tooling with the help of a computerized cabine that allows us to optimize it.
We manage and control the tooling with the help of a computerized cabine that allows us to optimize it.
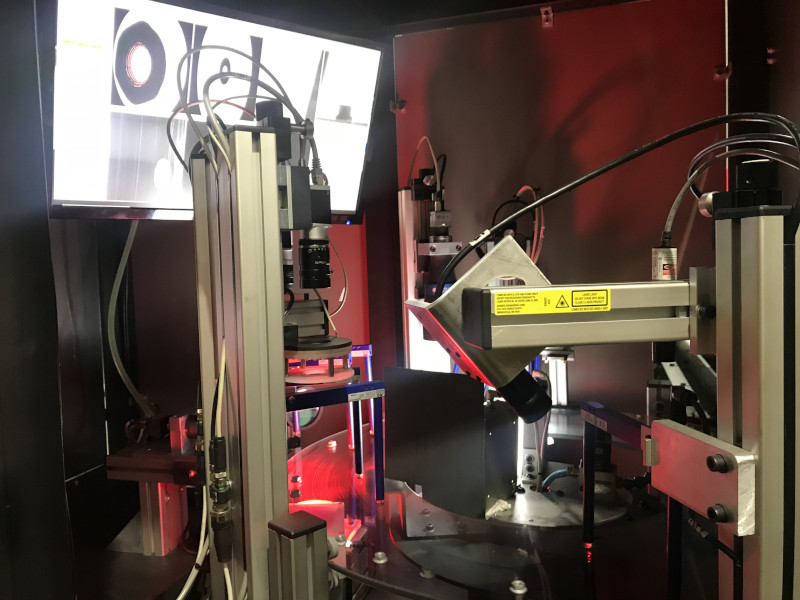
Sorting machines
To achieve our goal of 0 defects, we have five 100% sorting machines, divided into three groups:
The first group controls height and thread presence.
The second group comprises two 3D vision machines employing cameras with different types of lenses, allowing us to control the geometry of the part from different angles.
To achieve our goal of 0 defects, we have five 100% sorting machines, divided into three groups:
The first group controls height and thread presence.
The second group comprises two 3D vision machines employing cameras with different types of lenses, allowing us to control the geometry of the part from different angles.
The controlled dimensions are:
- Inner and outer Ø.
- Height.
- Internal shavings.
- Cracks and fissures.
- Thread presence.
- Presence of. protuberances.
- Deformities.
The third group consists of a control machine for screws and special parts with 360° control to check presence and geometry of external threads and for cracks all around the contour, as well as other cameras that check heights and inner and outer Ø.
The controlled dimensions are:
- Inner and outer Ø.
- Height.
- Internal shavings.
- Cracks and fissures.
- Thread presence.
- Presence of. protuberances.
- Deformities.